Ultimate Guide to Variable vs. Two-Stage Air Compressors
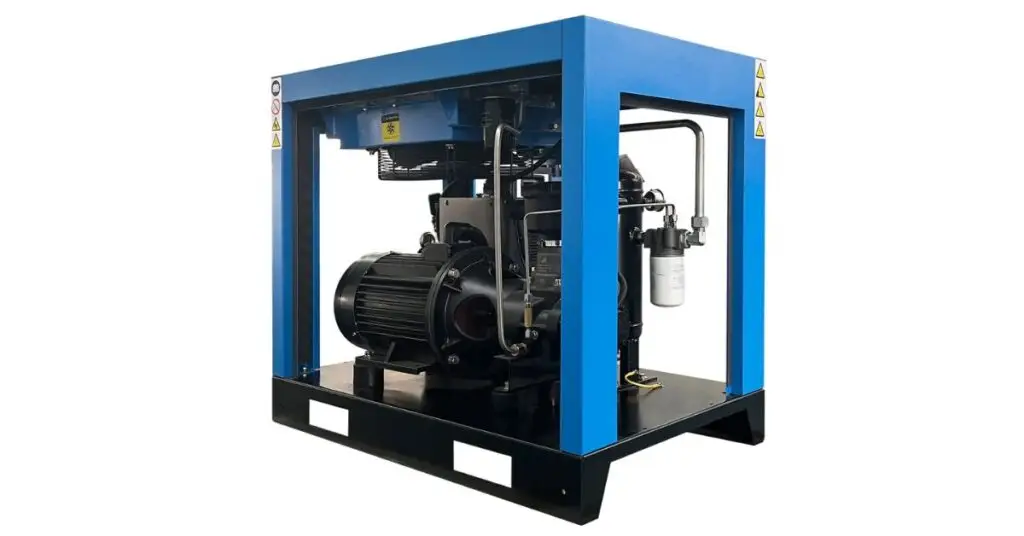
When it comes to industrial equipment, few tools are as versatile and essential as air compressors. Air compressors power a wide range of tools and machinery with unmatched efficiency. However, choosing the right type of air compressor isn’t a one-size-fits-all decision.
For businesses weighing their options, the debate often comes down to two contenders. This ultimate guide to variable versus two-stage air compressors discusses the key differences between them, helping you make an informed decision tailored to your needs.
What Are Air Compressors and Why Do They Matter?
Air compressors transform air into a powerful energy source to operate tools, inflate tires, spray paint, and much more. Their applications span various industries, including automotive repair, construction, manufacturing, and energy production, making them a vital piece of equipment across sectors.
While both variable and two-stage air compressors are highly effective, understanding their distinctions is crucial to selecting the right one for your specific requirements.
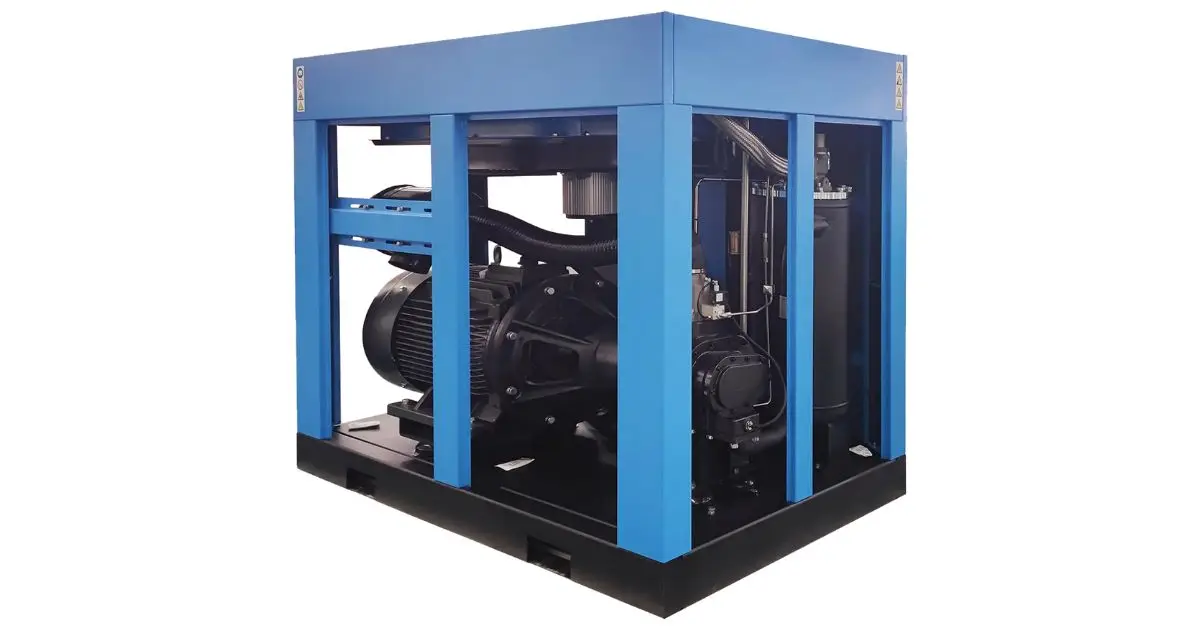
Exploring Air Compressors in Various Industries
Air compressors play a pivotal role in driving productivity and efficiency across industries. Here’s how they serve different sectors:
- Manufacturing. Power assembly lines, control automation tools, and maintain production efficiency.
- Automotive. Used for tire inflation, spray painting, and operating pneumatic tools like drills and impact wrenches.
- Construction. Essential for operating jackhammers, nail guns, sanders, and other heavy-duty equipment.
- Health care. Support critical applications like oxygen delivery systems and surgical equipment sterilization.
- Energy. Aid in drilling processes and turbine operation in the oil, gas, and renewable energy industries.
Choosing the right compressor type ensures seamless performance tailored to industry needs.
Understanding Variable Air Compressors
Variable air compressors, or variable speed drive (VSD) compressors, offer flexibility. Unlike fixed-speed models, these compressors modulate their motor speed to match specific air demand levels, making them highly energy-efficient. Here’s a closer look at their functionality and benefits.
How Variable Air Compressors Work
Variable air compressors adjust the speed of their motor based on the compressed air required at any given time. When demand is low, the motor slows down, conserving energy. Conversely, during peak demand, the motor ramps up to deliver the necessary pressure. This dynamic speed adjustment distinguishes them from traditional fixed-speed compressors.
Key Benefits of Variable Air Compressors
- Reduced motor speeds during low demand translate to lower energy consumption and significant cost savings.
- Maintain a steady air supply without fluctuations, ensuring consistent performance for sensitive equipment.
- Slower operation during low demand minimizes stress on internal components, extending the compressor’s lifespan.
- Energy-efficient operations reduce the carbon footprint.
Best Applications for Variable Air Compressors
Variable air compressors are ideal for businesses with fluctuating air demand. Industries like food processing, manufacturing, and printing, where air requirements frequently change, benefit immensely from their flexibility and cost-efficiency.
Exploring Two-Stage Air Compressors
Two-stage air compressors, as the name suggests, compress air in two stages to achieve higher pressure levels. These compressors offer reliability and the ability to handle intensive, high-volume tasks.
How Two-Stage Air Compressors Work
A two-stage compressor processes air in two steps. First, it compresses air to an intermediate pressure level and cools it. Next, it undergoes a second round of compression to reach the required pressure. This dual-stage process minimizes heat and ensures optimal performance.
Key Benefits of Two-Stage Air Compressors
- Perfect for applications requiring high-pressure air, such as industrial manufacturing and heavy-duty tools.
- Designed for rigorous, long-duration operation without overheating.
- Built to withstand demanding conditions, ensuring reliable performance over extended periods.
Best Applications for Two-Stage Air Compressors
Two-stage air compressors are common in industries that rely on heavy-duty equipment, such as construction, metalworking, and automotive manufacturing. Their ability to provide consistent, high-pressure air makes them indispensable for these applications.
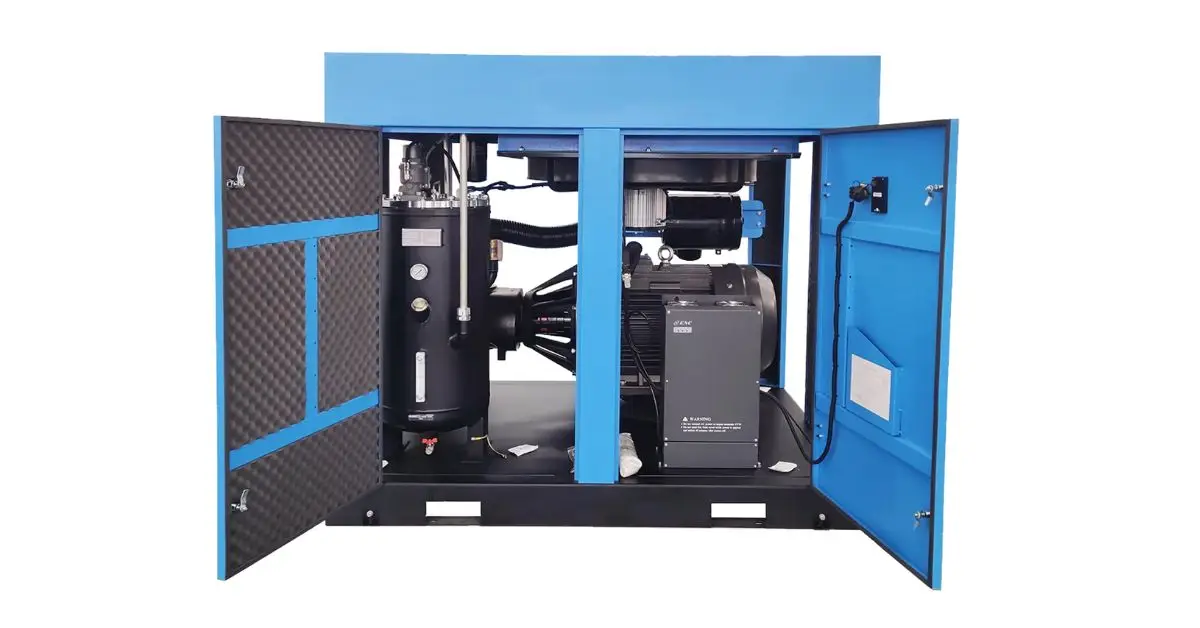
Variable vs. Two-Stage Air Compressors: A Direct Comparison
When deciding between variable and two-stage air compressors, the choice ultimately depends on your unique requirements. Here’s a checklist to help you decide:
- Determine whether your air usage fluctuates or remains consistent.
- Evaluate potential electricity savings from a variable compressor versus the cost of continuous high-pressure air from a two-stage model.
- Identify whether your work environment demands heavy-duty tools or energy efficiency.
- Factor in upfront costs and long-term energy and maintenance expenses.
- Ask yourself whether your team can handle the operation and maintenance of a more complex variable speed compressor or if a simpler two-stage model would be more suitable.
Making an informed decision ensures you invest in a compressor that meets your current and future needs.
Maintenance and Longevity
Regular maintenance is essential to ensure the longevity and efficiency of any air compressor. Here’s how maintenance differs for the two types.
Variable Speed Compressors
Variable speed compressors often require more specialized maintenance compared to simpler models. This is due to their advanced components, such as the variable frequency drive (VFD), which regulates motor speed and energy output. Regular inspections of the VFD, electrical connections, and cooling systems are crucial to prevent costly breakdowns.
Additionally, ensuring that the software controlling the compressor is up-to-date can improve efficiency and reduce wear on the system. While these units may demand more attention, proper maintenance can significantly extend their lifespan, making them a worthwhile investment for operations requiring flexibility and energy savings.
Two-Stage Compressors
Maintenance for two-stage air compressors is critical to ensuring their reliability and efficiency over time. Regularly checking the oil level and quality is essential, as proper lubrication prevents excessive wear on moving parts. Ensure that air filters are clean and replace them periodically to prevent contaminants from entering the system and reducing performance.
Additionally, drain the moisture from the tank daily to avoid rust and prolong the lifespan of the compressor. By adhering to a consistent maintenance schedule, operators can reduce downtime, improve performance, and extend the overall life of a two-stage air compressor.
Remember, proactive maintenance of your compressor equipment can improve operations and prevent costly downtime.
Make Your Investment Count
Both variable and two-stage air compressors offer unique advantages that cater to specific industrial needs. While variable compressors shine in their flexibility and energy efficiency, two-stage compressors excel in delivering high pressure for demanding applications. With this ultimate guide to variable versus two-stage air compressors, you can make the most of your investment.
If you’re still unsure which air compressor is right for you, you’ve come to the right place. At US Air Compressor, we understand your business needs inside and out. With our variable-speed compressor, you’ll have the perfect fit for your business needs.