How To Reduce Your Compressed Air System Costs
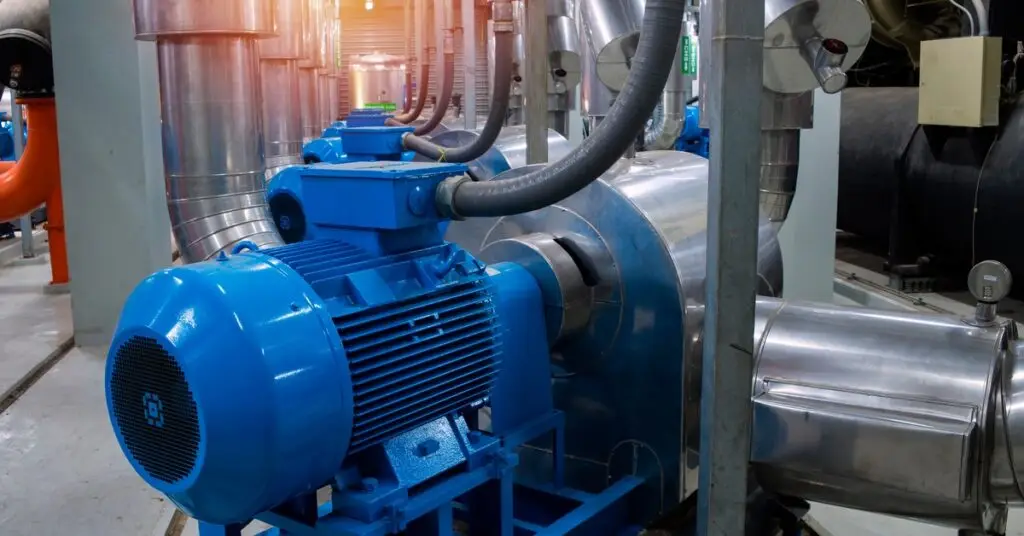
Compressed air systems are the backbone of many industries, from manufacturing to food processing. However, they’re notorious for their high operating costs, which account for a significant portion of a facility’s electricity usage. If left unchecked, these costs can take a toll on your business’s bottom line.
However, with compressed air systems, you don’t have to drain your budget. By understanding how to reduce your compressed air system costs, you can complete projects successfully while improving system performance.
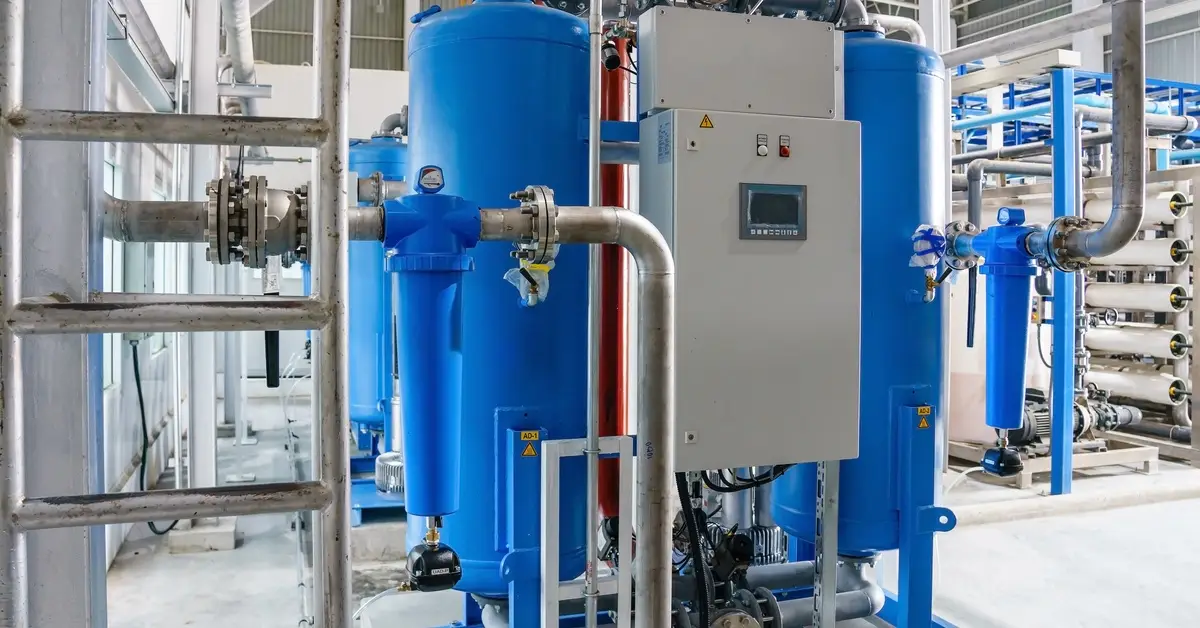
What Are Compressed Air Systems Used For?
Before we explore how to save costs, it’s important to understand just how important compressed air systems are across various industries. Here are some common use cases:
- manufacturing: operating pneumatic tools, assembly lines, and robotics
- food and beverage: powering food packaging, aerating liquids, and ensuring clean air in processing
- HVAC and refrigeration: supporting pneumatic actuators in heating, ventilation, and cooling systems
- pharmaceuticals: ensuring sterile air supply for sensitive production processes
- automotive: assisting in painting vehicles, tire inflation, and tool operation
- mining and construction: providing energy to heavy machinery, rock drills, jackhammers, and other tools
The ubiquity and versatility of compressed air systems make them indispensable, but these qualities also explain why their costs can pile up so quickly.
Major Cost Drivers in Compressed Air Systems
To reduce costs effectively, you must identify the main contributors to high expenses in compressed air systems. By addressing these areas, you set a strong foundation for operational cost savings.
Energy Consumption
Producing compressed air is an energy-intensive process, with inefficiencies often resulting in significant energy waste. Poorly maintained equipment, leaks, and improper system designs can escalate energy consumption and increase operational expenses.
Equipment Maintenance
Regular maintenance is crucial for keeping compressed air systems running efficiently and reliably. Maintenance tasks such as replacing filters, repairing leaks, and servicing compressors can add to operational costs.
Initial Investment
The upfront cost of acquiring compressors, air dryers, filters, and storage tanks constitutes a substantial initial investment. Depending on the size and complexity of the system, this capital expense can represent a major financial commitment for businesses.
Air Leaks
Air leaks are a pervasive issue in compressed air systems and contribute significantly to wasted energy. Even small leaks across a system can aggregate into considerable financial losses over time, elevating energy bills unnecessarily.
Inefficient System Design
An improperly designed compressed air system can lead to inefficiencies, including over-pressurization, inappropriate compressor sizing, and poor air distribution. These inefficiencies often result in higher energy usage and decreased equipment longevity, increasing overall costs.
System Downtime
System downtime due to equipment failure or maintenance can disrupt operations and lead to productivity losses. The costs associated with unplanned downtime can be severe, especially in industries reliant on continuous compressed air for critical processes.
Five Ways To Reduce the Costs of Your Compressed Air System
With costs on the rise, it’s always good to save money where you can. Here are a few best practices to follow when using compressed air.
1. Optimizing Air Compressor Settings for Efficiency
A frequently overlooked way to cut costs is by fine-tuning compressor settings. Even small adjustments can have a big impact over time.
Reduce Operating Pressure
Many systems run at higher-than-needed pressures, which wastes energy and shortens equipment lifespans. Lowering the pressure by just 2 psi can reduce energy consumption by 1 percent.
Align Air Supply With Demand
Use control systems to match compressed air output to actual demand. This prevents overproduction, reducing operating efforts.
Use Variable Speed Drives (VSD)
VSD-equipped compressors can adjust motor speed to match air demand in real-time, saving significant energy compared to fixed-speed systems.
Schedule Regular Maintenance
Maintaining equipment can improve efficiency and prevent costly breakdowns. Keep a maintenance schedule, and stick to it.
Consider Heat Recovery
Instead of releasing heat from compressors into the environment, use it for heating applications such as air or water heating.
By taking these factors into account, you can complete projects with less consumption and save money.
2. Implementing Leak Detection and Repair Programs
Air leaks in a compressed air system can lead to significant energy losses and increased operational costs. Implementing a leak detection and repair program helps identify and address leaks promptly, ensuring the system operates efficiently.
Use tools such as ultrasonic leak detectors to locate leaks and establish a routine inspection schedule to monitor new issues. Additionally, train staff to recognize common signs of air leaks, such as hissing sounds or pressure drops, to further enhance system reliability and reduce waste.
3. Making Energy-Efficient Equipment Upgrades
Upgrading to energy-efficient equipment is a critical step in reducing energy consumption and improving overall system performance. Replacing outdated components with modern, energy-efficient alternatives can lead to substantial cost savings and a smaller environmental footprint.
Look for equipment certified by programs like ENERGY STAR, as these products meet strict energy efficiency standards. Furthermore, consider investing in VSDs for motors, which optimize energy use by adjusting motor speed to match demand.
4. Leveraging Heat Recovery From Compressors
Heat recovery presents a valuable opportunity to improve energy efficiency in your facility. During the compression process, a significant amount of energy is converted into heat, which is often wasted.
By installing a heat recovery system, it is possible to capture this excess heat and repurpose it for other applications, such as heating water, spaces, or process fluids. Implementing heat recovery reduces energy waste and lowers operational costs and environmental impact, making it a smart solution for facilities aiming to enhance sustainability.
5. Monitoring and Maintenance
Consistent monitoring and maintenance are nonnegotiable for keeping costs down.IoT-based sensors, for example, can track system performance in real time, flagging inefficiencies or malfunctions before they become costly issues.
One maintenance task to stay on top of is maintaining filters.Dirty or clogged filters force compressors to work harder, increasing energy use. Clean or replace filters as needed.In addition, be sure to lubricate components. Proper lubrication prevents wear and tear, prolonging equipment lifespan and preventing breakdowns.
A proactive maintenance plan not only cuts costs but also enhances system reliability and longevity.

Tips for Choosing a Quality Compressed Air System
If you’re in the market for a compressed air system, here are some tips to ensure you make a cost-effective choice that meets your needs:
- Assess your demand. Calculate your facility’s peak and average compressed air requirements to select the appropriately sized system.
- Prioritize energy efficiency ratings. Look for systems with certifications like ISO 8573-1 to meet efficiency and quality standards.
- Consider total cost of ownership (TCO). Include upfront costs, maintenance, and energy consumption when comparing different systems.
- Seek expert guidance. Work with experienced providers who can tailor recommendations to your operations.
Whether you’re looking for a new compressed air system or upgrading an old one, a quality unit is the first step toward reducing costs.
The Payoff of Smart Compressed Air Management
A well-managed compressed air system can improve your bottom line while helping the environment. With these best practices, you can reduce your compressed air system costs and minimize overall waste. From optimizing system settings to upgrading to energy-efficient equipment, each step helps to deliver financial and operational benefits.
Are you ready to start reaping the rewards of more affordable compressed air systems? With US Air Compressor, you’ll have everything you need to reduce energy consumption. Check out our fixed-speed air compressor, and see how it can help you achieve a more cost-effective and sustainable future.