A Guide for Upgrading Your Air Compressor
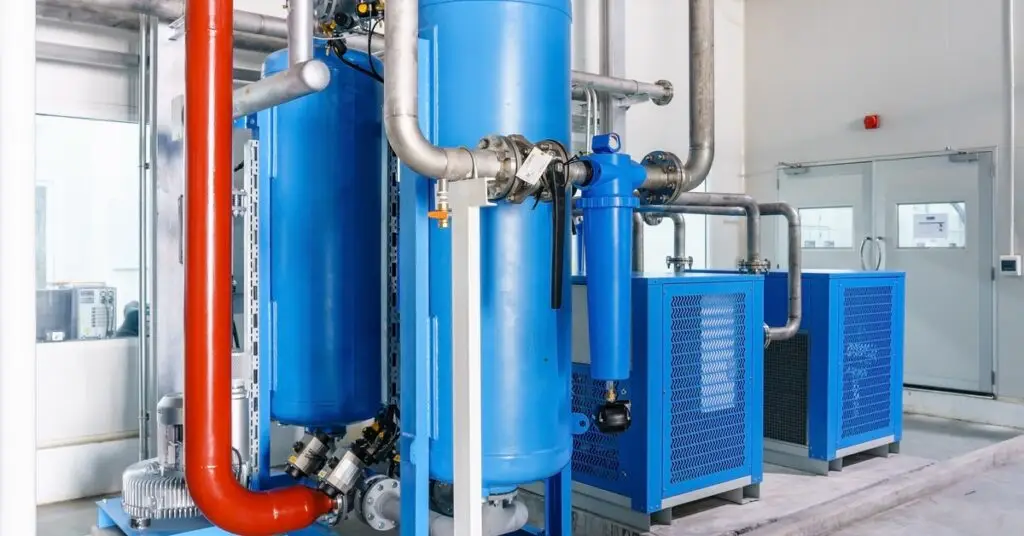
Upgrading your air compressor is a smart move when you want to improve efficiency, save energy, and tackle more demanding projects. No matter what you use this machine for, knowing when to upgrade your air compressor can bring immediate benefits to your workflow. Our guide for upgrading your air compressor will walk you through the process, from understanding your current setup to selecting the right enhancements and maintaining your system post-upgrade.
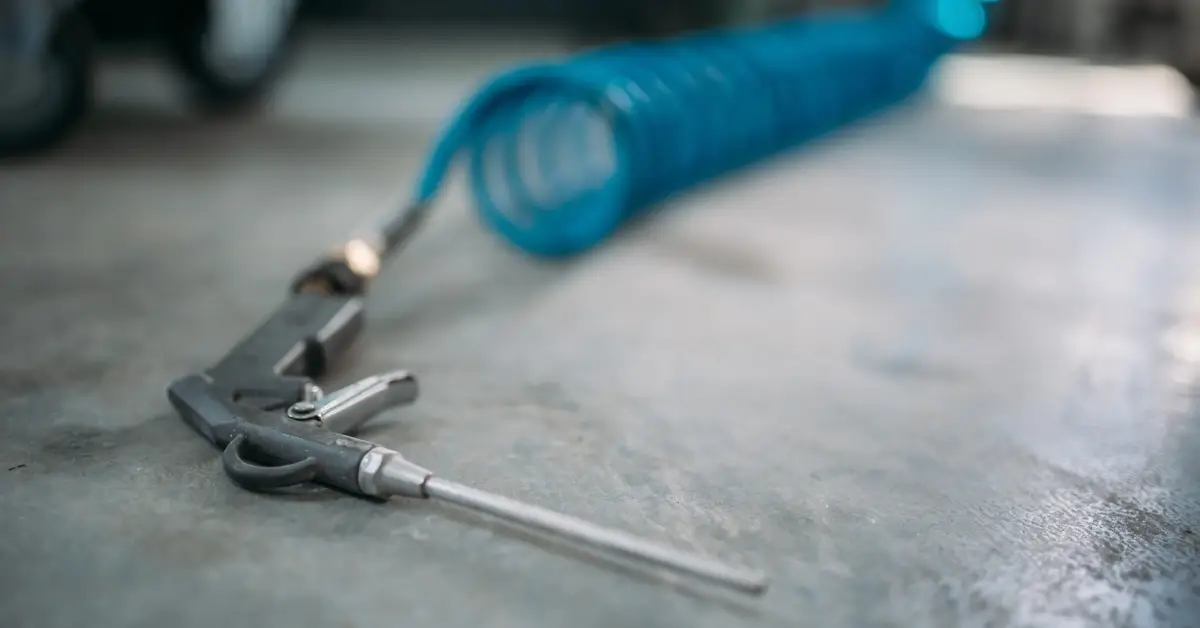
Assessing Your Current Air Compressor
Before jumping into upgrades, it’s important to take stock of your existing air compressor setup.
Evaluate Capacity and Performance
Start by assessing whether your air compressor meets your current needs. Ask yourself these questions:
- Does the machine struggle to maintain consistent pressure during demanding projects?
- Does it frequently run out of air?
- Is the unit too noisy or energy-inefficient?
Knowing where your current compressor falls short will help you identify the features that need to be addressed.
Identify Usage Patterns
How often do you use your air compressor, and for what types of tasks? A weekend DIYer will need different device features compared to someone operating a pneumatic assembly line. Evaluate your workflow and match it with the air compressor performance you’re envisioning.
Check for Wear and Tear
Older compressors may show signs of wear, such as reduced efficiency, leaks, or overheating. Inspect components such as hoses, seals, and gauges, as these wear out the fastest and may hold back your compressor’s performance.
Focusing on the Right Upgrades
Once you assess your current system, you can focus on the upgrades that will make the most impact.
Tank Size
If your machine frequently runs out of air, a larger air tank may be useful, allowing for longer periods of continuous use without requiring the compressor to cycle as often. This is especially beneficial for tasks that demand consistent airflow or higher air volume.
Conversely, smaller tanks may suffice for less intensive applications, where portability and space-saving are prioritized. Evaluating your usage patterns will guide you in selecting the appropriate tank size for maximum efficiency and performance.
Motor and Pump
Upgrading to a more powerful motor or pump can significantly boost airflow (CFM) and pressure output (PSI). Higher CFM and PSI ratings optimize your compressor for demanding tools like spray guns, impact wrenches, and sanders.
When selecting an air compressor, consider the horsepower (HP) of the motor and the CFM rating of the pump. Higher HP typically means the compressor can handle more demanding tasks, while a higher CFM ensures quicker air delivery.
Air Dryer
Adding an air dryer to your system is an essential upgrade if you work in environments where moisture in compressed air can cause problems. An air dryer removes excess moisture from the air, preventing issues like rust in tools, contamination in paint applications, and reduced efficiency of pneumatic equipment. Various types of air dryers are available, including refrigerated and desiccant models, allowing you to choose the best option for your specific needs.
Automatic Drain Valve
An automatic drain valve is another essential component for maintaining the efficiency and longevity of your air compressor system. This device works by automatically expelling accumulated moisture and contaminants from the air tank or system at regular intervals for consistent performance.
Unlike manual drain valves, which require regular user intervention, automatic valves save time and reduce the chance of human error. They’re especially useful in high-demand environments where the system operates continuously, as they help prevent corrosion, blockages, and damage caused by excess moisture.
Pressure Regulator
A pressure regulator is a vital component in many pneumatic and hydraulic systems, ensuring stable and consistent pressure levels within the system. It works by maintaining the output pressure at the desired level, regardless of fluctuations in input pressure or changes in flow demand.
This stability is crucial for optimizing system performance, preventing equipment damage, and maintaining safety. Pressure regulators come in various types designed for specific applications, such as single-stage or dual-stage regulators, and are commonly used in industries ranging from manufacturing to medical devices.
Smart Features
Modern air compressors offer features like digital controls and automated performance monitoring. These enhancements are perfect for professionals looking to optimize efficiency and convenience.
Digital controls allow for precise pressure adjustments and easy monitoring of key metrics, while automated performance monitoring can detect potential issues before they become costly problems. Consider these upgrades if you want to take your air compressor setup to the next level.
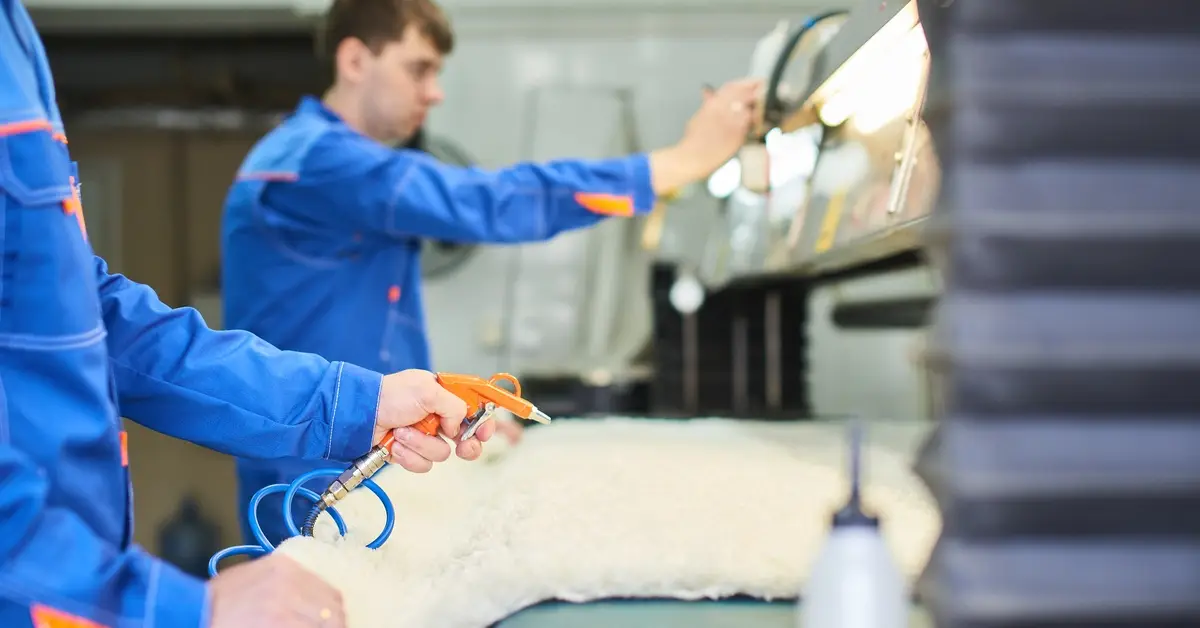
Following a Step-by-Step Upgrade Guide
Upgrading your air compressor doesn’t have to be a daunting task. Here’s a straightforward guide to get you started.
1. Choose the Right Components
Evaluate which upgrades are most critical for your needs. Consider consulting your manufacturer’s recommendations to ensure part compatibility with your current setup.
2. Gather Your Tools and Materials
Before making modifications, collect the necessary tools. For example, wrenches, screwdrivers, and Teflon tape are essential for installing new components like hoses or regulators.
3. Disconnect and Depressurize
For safety, turn off your air compressor and release any stored air by opening the drain valve. This step prevents accidents while working on the unit.
4. Install Upgrades Piece by Piece
Follow your equipment manuals to carefully install each new component. If you’re upgrading the tank, motor, or pump, additional time and adjustments may be required for a proper fit.
5. Reconnect and Check for Leaks
Once installed, reconnect hoses and fittings tightly, but avoid over-tightening. After starting up your system, listen for air leaks and inspect the connections.
Testing and Maintaining the Air Compressor
After completing your upgrades, test your air compressor under regular working conditions. Routine testing and maintenance ensure your system operates efficiently and safely. Begin by running the equipment at full capacity while monitoring for irregular performance, noises, or vibrations.
Inspect all connections, belts, and moving parts to confirm they are secure and functioning properly. Clean or replace filters as necessary to maintain optimal airflow. Additionally, schedule periodic maintenance checks to address wear and tear before it becomes a significant issue. Proper care will extend the lifespan of your system and minimize downtime.
Turbocharging Your Workflow With a New Compressor
Modern air control systems make your workflow more efficient, saving energy and getting projects done with ease. By following this guide for upgrading your air compressor, you can assess, enhance, and maximize your system to meet your needs.
If you’re ready to step into a more efficient workspace, contact the professionals at US Air Compressor. Our two-stage compressor will allow you to complete projects without hassle. Reach out to our team for expert advice and recommendations to make the upgrade process smoother.