A Guide to Accurately Sizing or Replacing Air Compressor Tanks
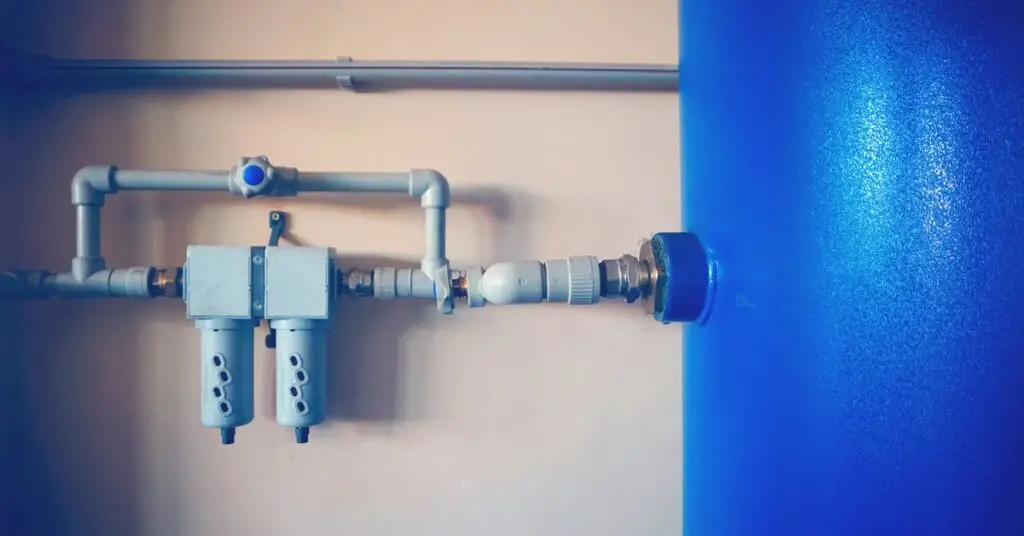
Choosing the right air compressor tank size can make or break your workflow. Whether you’re replacing an older tank or purchasing one for a new system, proper sizing ensures optimal efficiency, performance, and safety. But how do you ensure your air compressor tank is the right size? And when is it time to replace an old one?
To answer these questions and more, we’ve put together this guide to accurately sizing or replacing air compressor tanks. Armed with this knowledge, you’ll know how to choose the right tank for your needs, replace it when necessary, and maintain it for maximum longevity.
Types of Air Compressor Tanks and Their Uses
Air compressor tanks are primarily categorized by their configuration and intended use. Here are the main types to consider:
Horizontal Tanks
These are common in high-demand environments like workshops and factories. They’re stable and suitable for applications requiring higher capacities.
Vertical Tanks
Ideal for tight spaces, they take up less floor space, making them a smart choice for smaller setups.
Portable Tanks
Designed for mobility, these smaller tanks are perfect for home users or contractors who need compressed air on the go.
Factors Influencing Tank Size
Selecting the perfect size for an air compressor tank depends on multiple factors. Here’s what to consider.
1. CFM Requirements for Your Tools
CFM (cubic feet per minute) measures the air demand of your tools. Tools like sanders, impact wrenches, and paint sprayers have varying CFM needs. Always sum up the total CFM required by your tools and choose an air compressor tank that exceeds this number slightly.
2. Duty Cycle Considerations
Consider how often your air compressor will run during an average operation. A higher duty cycle means the compressor runs more frequently, potentially requiring a larger tank to prevent wear and overheating.
Generally, a 50 percent duty cycle uses the compressor half the time and relies heavily on adequate tank storage, while a 100 percent duty cycle may require larger compressors capable of continuous operation.
3. Space Constraints and Portability
If you operate in a limited space, a vertical tank is likely your best bet. If portability is crucial, a smaller, lightweight tank will serve you well. Balance storage capacity needs with available space to make the right choice.
Step-by-Step Guide to Sizing an Air Compressor Tank
Follow these steps to determine the perfect air compressor tank size for your needs.
Step 1: Calculate Total CFM Needs
List all the tools you’d use simultaneously and add their CFM ratings. This total is your baseline air requirement.
As an example, if you have an impact wrench with a 5 CFM rating, a spray gun at 8 CFM, and a grinder at 6 CFM, you have a total CFM of 19.
Step 2: Determine Optimal Storage Capacity
Air compressor tanks are measured in gallons. Larger tanks (60-80 gallons) are suitable for industrial applications, while smaller tanks (20-30 gallons) are ideal for lighter work.
Step 3: Account for Future Tool Additions
If you plan to expand your toolkit, it’s wise to go for a slightly larger tank. This future-proofs your setup and saves extra expenses down the line.
Tips for Purchasing an Air Compressor Tank
When it’s time to make a purchase, keep these tips in mind:
Tip 1: Consider Portability
If you need to move your air compressor frequently, opt for a smaller tank with wheels or a handle. This ensures ease of transportation while maintaining efficiency for lighter tasks.
Tip 2: Check Material Durability
Tanks made from durable materials such as steel or aluminum can withstand wear and tear. Aluminum tanks are lightweight and resistant to rust, while steel tanks are sturdier, making them suitable for heavy-duty use.
Tip 3: Verify PSI Compatibility
Ensure the tank can support the maximum pressure (PSI) required by your tools. A tank with insufficient PSI may cause your tools to underperform or fail completely.
Tip 4: Assess Storage Space
Before purchasing, measure your available storage area to make sure the tank fits comfortably. Compact tanks work better in tight spaces, while larger tanks require more room to accommodate.
Tip 5: Review Noise Levels
Some tanks are designed with noise reduction features. If you’re working in a shared space or noise-sensitive environment, choose a tank specifically marketed as quiet or low-noise.
Replacing a Tank
Over time, your compressor tank may need to be replaced due to wear, corrosion, or other damage. Regularly inspect your tank for any visible signs of deterioration, such as rust, cracks, or leaks, which may indicate the need for a replacement.
When to Consider a Replacement?
- Visible rust or corrosion: This weakens the structure and creates safety risks.
- Leaks: Persistent air leaks signal that the tank has reached the end of its lifespan.
- Frequent pressure failures: If your tank struggles to maintain pressure, it might be time for a replacement.
Steps to Replace a Tank
By following these steps, you can maintain the efficiency and safety of your air compressor system. Always consult the manufacturer’s instructions for specific replacement guidelines.
Turn Off Power and Release Pressure
First, ensure the compressor is completely powered down, and release all air pressure from the tank for safety.
Disconnect Hoses and Attachments
After that’s done, you can safely remove all hoses, attachments, and fittings connected to the tank.
Remove the Old Tank
Detach the old tank according to the manufacturer’s guidelines. This may require unbolting it from the compressor unit.
Install the New Tank
Next, secure the new tank in place and reconnect all necessary hoses and attachments. Ensure all connections are tight to prevent any leaks.
Test the System
Finally, power up the compressor and monitor it closely to verify the new tank is functioning correctly and safely. Remember to always consult the manufacturer’s instructions for specific replacement guidelines.
Maintenance Practices for Longevity
An air compressor tank can serve you for years if properly maintained. Follow these tips to extend its lifespan.
Regular Draining
Moisture buildup promotes rust. Use the drain valve to release excess water after each use, especially in humid environments.
Inspect for Leaks and Damage
Perform routine visual checks to identify small leaks, cracks, or dents before they escalate into larger issues.
Use Rust-Proof Coatings
Apply rust-proof coatings to extend the life of steel tanks, particularly in settings where moisture exposure is high.
Ensure Proper Storage
Store the compressor tank in a cool, dry, and well-ventilated area to minimize condensation and corrosion risks.
Invest in Tank Accuracy and Efficiency
Finding a new compressor tank may seem challenging, but the payoff is well worth it. With the right size tank, you’ll enjoy smoother operations, prolonged tool life, and better efficiency. With so much to consider, having a guide to accurately sizing or replacing air compressor tanks will ensure you’re ready for whatever comes your way.
Whether you’re a DIY enthusiast or a seasoned professional, getting it right makes all the difference. If you need more help with your air compressor tools, US Air Compressor is here with the latest parts and components. Check out our variable frequency drive compressor and see the results for yourself!