Heatless Adsorption vs. Heated Adsorption Air Dryers
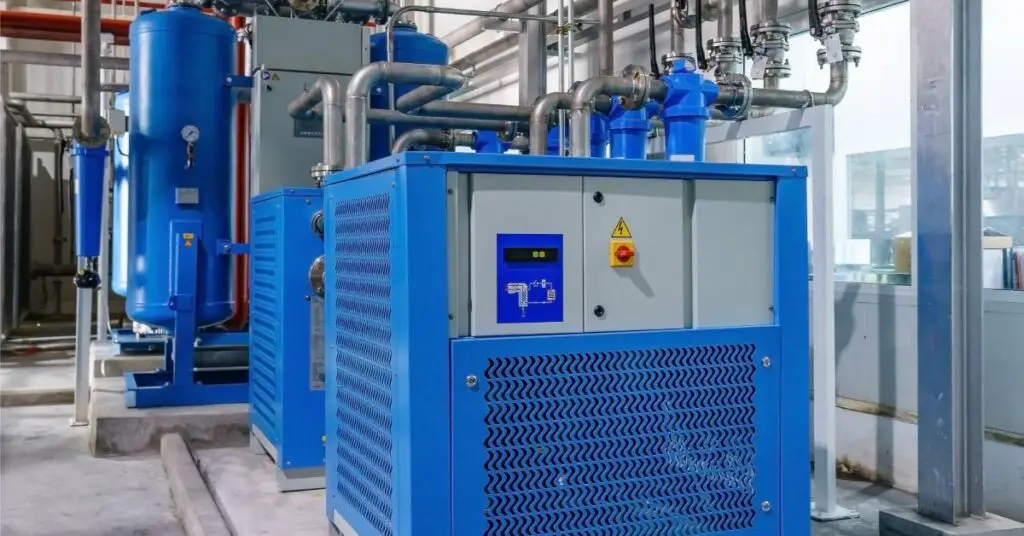
Effective air drying is critical in industries where it has a direct impact on production efficiency, product quality, and equipment longevity. The choice of air dryers is central to meeting operational demands for many facilities, from manufacturing plants to pharmaceutical labs. Among the most common options are heatless adsorption air dryers and heated adsorption air dryers. Industries use both widely, yet they greatly differ in their approach.
This blog post offers an in-depth review comparing heatless adsorption and heated adsorption air dryers and details how they work and how to choose one that’s right for you. By the end, you’ll gain a clear understanding of each method, its applications, and emerging trends transforming how businesses operate.
The Basics of Adsorption Air Dryers
Adsorption air dryers function by removing moisture from compressed air, ensuring that it meets the required levels of dryness. This process is particularly important in food processing, electronics, and chemical production where excess moisture can lead to product damage, equipment wear, and increased maintenance costs. The following sections detail the two primary types of adsorption air dryers: heatless and heated.
Heatless Adsorption Air Dryers
These dryers use a simple yet effective mechanism. They rely entirely on the compressed air system itself for the regeneration cycle. A portion of the dried air—known as purge air—strips moisture from the desiccant material, allowing it to regenerate for reuse. This method requires no external heat source, making the dryers relatively straightforward to operate.
Heated Adsorption Air Dryers
Heated dryers utilize an external heat source to regenerate the desiccant. This system significantly reduces the amount of purge air needed compared to heatless models. Depending on the specific system’s design, the heating mechanism can use electricity or steam as a power source.
Both types aim for the same result: dry, moisture-free air. However, each presents distinct advantages and shortcomings that you should know about before making a purchase.
Heatless vs. Heated Adsorption Air Dryers: Key Differences
Here’s a closer look at how these two air dryer types compare in terms of energy efficiency, operational costs, and environmental impact.
1. Energy Efficiency
Heatless adsorption air dryers are less energy-efficient because they rely heavily on compressed air (purge air) for desiccant regeneration. It can divert approximately 15-20% of the dryer’s capacity for this purpose. While these air dryers consume no additional energy for heating, the loss of compressed air can reduce overall system efficiency.
Heated adsorption air dryers, in contrast, benefit from reduced purge air consumption due to their external heating mechanism. While they consume electrical or thermal energy for heating, the savings in compressed air often balance out or outweigh these added energy costs.
2. Operating Costs
Heatless dryers are simpler to maintain, as they do not have heating elements or complex components, leading to lower upfront and ongoing costs. However, their reliance on significant purge air may translate to higher associated operational costs, especially in demanding environments.
Heated dryers have higher initial investments because of their sophisticated design. They also incur additional costs for electricity or steam. Despite the incurred costs, heated dryers’ reduced need for purge air can make them cost-effective in the long run, particularly for high-volume setups.
3. Environmental Impact
Heatless dryers are ideal for businesses aiming to avoid additional carbon emissions from external heating systems. However, their compressed air inefficiency can result in increased energy demands elsewhere in the production chain.
Heated dryers tend to have a larger carbon footprint due to their energy needs. That said, modern heated dryers often use energy-efficient heating technologies, reducing their overall environmental impact.
Real-World Applications of Heatless vs. Heated Dryers
Each type of adsorption air dryer can address specific use cases. Here are some practical examples of where they shine.
Heatless Adsorption Air Dryers
- Small to medium-scale operations with intermittent air-drying needs.
- Environments lacking access to consistent or affordable external heat sources.
- Critical industries that require simple and reliable air-drying solutions, such as medical facilities and pharmaceutical labs.
Heated Adsorption Air Dryers
- Large-scale manufacturing facilities with high compressed air demands.
- Operations that can use energy recovery systems to offset heating costs.
- Petrochemical, automotive production, and similar industries that prioritize energy optimization.
It may be time to upgrade for better efficiency and production times if any of these examples match your needs.
Factors To Consider When Choosing Between Heatless and Heated Adsorption Air Dryers
Evaluating several factors is essential when deciding which system is right for your business. Consider the following factors:
- Initial investment: Heatless dryers are generally more affordable upfront, while heated dryers require a higher initial cost for installation and setup.
- Maintenance requirements: Heatless models are simpler and easier to maintain, while heated systems may demand more frequent or specialized servicing due to their additional components.
- Air quality needs: Assess the desired dew point of your compressed air. Heatless dryers tend to be sufficient for standard moisture-removal requirements, while heated dryers excel in environments requiring ultra-dry air.
- Energy costs: Consider your local energy rates. Heated dryers may offer better long-term savings in areas with moderate electricity costs, whereas heatless systems work better in regions where compressed air is readily available.
- Space and infrastructure: Evaluate your facility’s space and setup. Heated systems typically require more room for the external heating mechanism and additional infrastructure.
Accounting for these needs can help you make an informed decision about which air dryer is right for your environment.
Future Trends in Air Dryer Technology
The air dryer industry is rapidly evolving, with advancements expected to impact heatless and heated systems. Some emerging trends include:
- Energy-efficient systems: Variable purge control in heatless dryers and energy-saving heating mechanisms in heated models are reducing operational costs and environmental impacts.
- IoT and automation: Smart air dryers equipped with IoT sensors and automated controls can optimize performance and provide predictive maintenance alerts.
- Hybrid models: These dryers blend the best features of heatless and heated technologies into a single solution.
- Material science advancements: Improved desiccant materials with higher moisture-absorbing capacity and longer lifespans, enhancing the adsorption air dryers’ efficiency.
With so many developments, it’s easy to see why these technologies have become so popular within the manufacturing sector.
Making the Right Choice for Your Business
Heatless adsorption and heated adsorption air dryers have their merits, but the best choice ultimately depends on your specific operational needs, budget, and sustainability goals. Understanding the core differences between these two systems will help you make a decision that works for you, whether you prioritize simplicity and ease of maintenance or advanced efficiency and long-term cost savings.
Keeping the air clean and dry is crucial for maintaining productivity and quality across all industries. Luckily, US Air Compressor has you covered. Our wide selection of products is sure to have something that fits your operational goals if you’re in need of an industrial air dryer for your compressor. Find a system that sets your business up for long-term success!